
Protecting Perovskite Solar Cells from Water Vapor-Induced Degradation
In recent years, organometal halide perovskites have become the most promising class of next generation solar materials due to their extremely high efficiencies (>20%), their amenability to cheap manufacturing and the potential for >40% efficiency when paired with other solar technologies.4–6. With their relative ease of fabrication, potential for roll-to-roll processing and extremely high efficiencies, perovskite solar cells (PSC) could be a disruptive technology that would put the world on track to meet its targets for solar energy production. While still in its infancy the exciting commercial potential of PSC is already evidenced by the founding of companies in the U.S. and worldwide that seek to commercialize the technology.
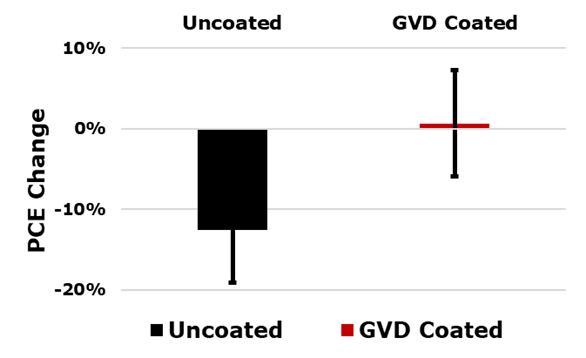
Potential manufacturers of PSCs face the challenge of dealing with the water vapor sensitivity of perovskites.7–10 Even setting aside the need for packaging technologies to provide the necessary module longevity in operation, PSC degradation during the manufacturing process due to environmental exposure is a significant obstacle to PSC commercialization and threatens to jeopardize their entry into the market. Production must be done in dry conditions to ensure reliable high performance. The cost impact of this requirement is high, and it could be a major obstacle to realizing the benefits of the PSC technology.
In a DOE funded Phase I and Phase II SBIR project, GVD validated the use of the barrier coating in protecting perovskite solar cells from water vapor. By integrating a barrier coating step following application of the back contact during PSC manufacturing a PSC manufacturer could eliminate the need to perform subsequent steps in a dry environment. GVD showed that the barrier coating, applied directly atop methylammonium lead iodide photovoltaic stacks from a U.S. hybrid perovskite-silicon solar cell company, eliminates degradation for up to 2 days at 85% RH with no other encapsulation. The coating is compatible with subsequent manufacturing steps, such as EVA lamination. GVD’s coating is transparent in the visible spectrum, including >99.9% transparent in the critical window for perovskite-silicon hybrids (780-1100 nm). It undergoes no yellowing after UV-exposure equivalent to a 25 year field lifetime. Alleviation of dry processing requirements, even for a few major steps, could reduce required CAPEX and would accelerate the global installation of solar energy to meet climate targets.
GVD’s barrier coatings have a water vapor transmission rate ~100x lower than that of the industry standard encapsulation material for silicon solar cells, ethylene vinylacetate. GVD’s process yields coatings with similar performance to that of sputtered or oxide-only CVD processes, but, unlike sputtering or oxide-only depositions, GVD’s process inflicts no damage on the solar cell. GVD’s coatings have very high thermal stability (up to 200 °C continuous use) and excellent UV-stability, which makes them far more suitable as part of a field-deployed solar cell module than polymer coatings.